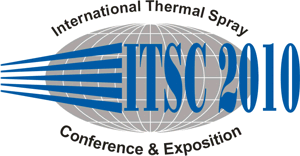 |
Abstract No.: |
|
Scheduled at:
|
Tuesday, May 04, 2010, Sophia Room 2:15 PM Young Scientists
|
|
Title: |
Columnar structured thermal barrier coatings by thin film low pressure plasma spraying (LPPS-TF?)
|
|
Authors: |
Andreas Hospach* / Forschungszentrum Jülich GmbH, Institut für Energie- und Klimaforschung (IEK-1), Germany Georg Mauer / Forschungszentrum Jülich GmbH, Institut für Energieforschung (IEF-1), Germany Detlev Stöver/ Forschungszentrum Jülich GmbH, Institut für Energieforschung (IEF-1), Germany Robert Vaßen/ Forschungszentrum Jülich GmbH, Institut für Energieforschung (IEF-1), Germany
|
|
Abstract: |
The very low pressure plasma Spray (VLPPS) process has been developed with the aim of depositing uniform and thin coatings with large area coverage by plasma spraying. At typical pressures of 100-200 Pa, the characteristics of the plasma jet change compared to conventional low pressure plasma spraying processes (LPPS) operating at 5-20 kPa. The combination of plasma spraying at low pressures with enhanced electrical input power has led to the development of the LPPS-TF? process (TF = thin film). Applying the O3CP gun at electrical currents up to 2.5 kA an input power level of 150 kW is achieved. At appropriate parameters it is even possible to evaporate the powder feedstock material providing advanced microstructures of the deposits.
This technique offers new possibilities for the manufacturing of thermal barrier coatings (TBCs). Besides the material composition, the microstructure is an important key to reduce thermal conductivity and to increase strain tolerance. In this regard, columnar microstructures deposited from the vapor phase show considerable advantages. Therefore, physical vapor deposition by electron beam evaporation (EB-PVD) is applied to achieve such columnar structured TBCs. However, the deposition rate is low and the line of sight nature of the process involves specific restrictions.
In this paper, the deposition of thermal barrier coatings by the LPPS-TF? process is shown. It is investigated how the evaporation of the feedstock powder could be improved and to what extend the deposition rates could be increased. Amongst others, yttria stabilized zirconia coatings are highlighted.
|
|