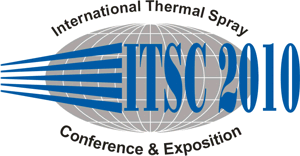 |
Abstract No.: |
|
Scheduled at:
|
Tuesday, May 04, 2010, Olivia Room 9:20 AM Plasma Spraying 2
|
|
Title: |
Influence of feedstock powder for fabrication of aluminum nitride in reactive atmospheric plasma spray process
|
|
Authors: |
Mohammed Shahien* / National Institute of Advanced Industrial Science and Technology, Japan Motohiro Yamada / Toyohashi University of Technology, Japan Toshiaki Yasui/ Toyohashi University of Technology, Japan Masahiro Fukumoto/ Toyohashi University of Technology, Japan
|
|
Abstract: |
Aluminum nitride (AlN) is attractive material due to its outstanding properties: high thermal conductivity (up to 320 W/mK) and high electrical resistivity. Therefore, AlN thermal sprayed coating is a promising component electrical and electronic application. However, it is difficult to fabricate AlN coatings directly by conventional thermal spray processes due to thermal decomposition of AlN powder during spraying. In order to fabricate AlN coatings, reactive plasma spraying is a promising process, in which metal powders react with surrounding active species in plasma. In our previous studies, it was possible to fabricate AlN based coating by Radio Frequency plasma spray system. However, it was difficult to fabricate dense coating due to low particle velocity in the RF plasma system. Furthermore, the RF plasma spray was carried out in vacuum ambient. In this study, feasibility of atmospheric plasma spray process for fabrication of AlN coating and the nitriding process of the feedstock powder were investigated. Pure aluminum powder injected into N2/H2 plasma and deposited onto steel substrate. It was possible to fabricate cubic-AlN based coating through the reaction between Al powder and the plasma in APS system. The fabricated coating was about 100 ìm thickness and 1020 Hv hardness. The concentration ratio of AlN in the coatings was increased with the spray distance. However, the thickness of the coatings decreased with the spray distance. It was confirmed that nitriding reaction occurred both during flight in the plasma and after deposit on the substrate. The process was optimized through investigating the influence of feedstock powder and changing the particle size and controlling the spray parameters.
|
|