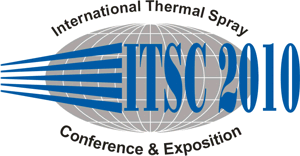 |
Abstract No.: |
|
Scheduled at:
|
Tuesday, May 04, 2010, Olivia Room 10:40 AM Hard Chrome Replacement
|
|
Title: |
APS-Al2O3 coatings versus arc sprayed and plasma anodized Al layers
|
|
Authors: |
Thomas Grund / Institute of Materials Science and Engineering, IWW, Chemnitz University of Technology, Deutschland Thomas Lampke* / Institute of Metrials Science and Engineering, Germany Daniel Meyer/ Institute of Metrials Science and Engineering, Germany Hanna Pokhmurska/ Institute of Metrials Science and Engineering, Germany Bernhard Wielage/ Institute of Metrials Science and Engineering, Germany
|
|
Abstract: |
Thermally sprayed alumina coatings are widely used in a range of industrial applications to improve wear and erosion resistance, corrosion protection and thermal insulation of metallic surfaces. These properties are required for many components for production processes in the paper and printing industry. By means of efficient and adjustable coating processes, long-term use of the refined surfaces is obtained. It can be seen that cost-efficient arc-sprayed Al2O3 coatings post-treated by plasma-electrolytic oxidation (PEO) form layers with outstanding hardness, bonding strength, abrasion and corrosion resistance as well as extended service time. The generated layers (arc-sprayed and PEO-converted) show a thickness of up to 250 µm and a microhardness of up to 1600 HV0.1. These coatings are designed to partially replace hard chromium. The oxide nucleation begins at energetically preferred sites at the surface and forms a non-porous barrier layer. Then the formed oxide layers are partly melted and additional high-temperature phases at the oxide/electrolyte interface, like spinel or mixed oxides, are formed. This rapid oxide formation process stops when the electric field strength falls under a critical value self-induced by the growing layer thickness. In general, the achieved composition and properties depend on the substrate phase composition, the electrolyte composition, and the treatment regimes (temperature, processing time, voltages, current densities, current forms AC/DC etc.). In conclusion, different substrates coated by thermal spraying of aluminium and other valve metals can be converted by PEO to fully or partially oxidized surfaces with outstanding properties. In the presented article, these coatings will be mechanically and chemically evaluated and compared to standard APS-Al2O3 coatings.
|
|